At the recent Land Oilfield Equipment Upgrade Seminar, industry professionals and oilfield enterprise leaders gathered to witness the future of drilling: a fully modular land oil rig capable of rapid deployment and deconstruction. This hands-on demonstration, centered around a physical scale model, showcased a new era in oil rig construction and design that aims to minimize operational delays while maximizing extraction efficiency and cost-effectiveness.
Modular Oil Rig Design: A Breakthrough in Efficiency
The highlight of the seminar was the live demonstration of a modular oil rig system. Unlike traditional rigs, which require extensive on-site construction and multiple logistical stages, this innovative model features prefabricated components that are built offsite, transported with ease, and assembled on location with minimal time and labor.
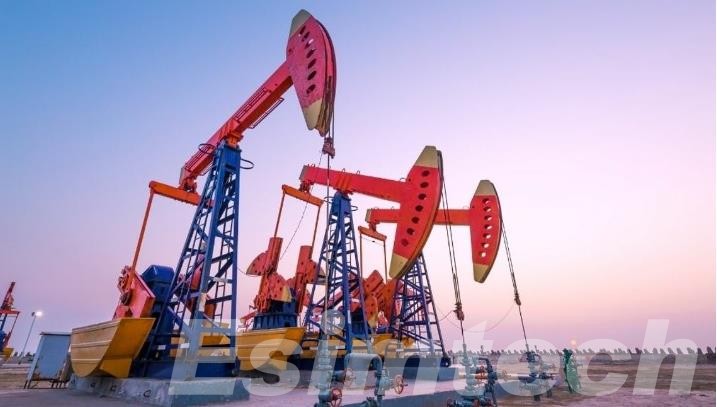
This design greatly streamlines the oil rig construction process. With each section—such as the derrick, substructure, mud pumps, and control systems—engineered for plug-and-play assembly, operators can significantly reduce rig-up time from weeks to just a few days. The modular architecture also simplifies the rig-down process, allowing for faster relocation and minimizing downtime between drilling projects.
Faster Assembly, Lower Costs
One of the key pain points in conventional land rig deployment is the logistical overhead. Transporting a complete drilling system across rugged terrain typically demands large convoys, significant manpower, and high fuel consumption. Modular design addresses these issues head-on. By breaking the rig into compact, containerized units, the transport footprint is reduced, lowering both emissions and costs.
During the seminar, engineers demonstrated how each rig module was designed for quick locking mechanisms and integrated power connections. Attendees witnessed how the derrick was raised using hydraulic jacks and anchored in under 30 minutes. This speed not only saves time but also improves safety by reducing manual labor and exposure to hazards.
Data-Driven Efficiency Gains
Accompanying the live rig demonstration was a detailed presentation of field data comparing pre- and post-upgrade performance across several sites. The results were impressive: upgraded rigs featuring the modular architecture showed up to 28% shorter installation times and 15% reductions in energy consumption. Moreover, extraction throughput improved due to optimized pipe handling and real-time system diagnostics integrated into the modular control center.
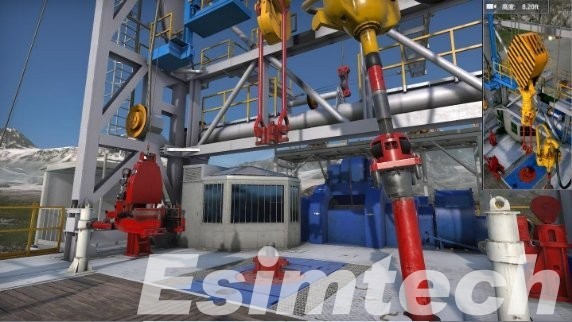
Much of this performance increase is tied to improvements in the oil rig design itself. By incorporating smart automation modules and improved hydraulic layouts, the system delivers better torque control, drilling accuracy, and wear resistance, even under prolonged use. These features are essential for reducing maintenance frequency and ensuring uptime in demanding environments.
Training & Simulation Support
In parallel with hardware upgrades, seminar organizers emphasized the importance of crew training. To this end, Esimtech introduced simulation-based training platforms that allow teams to rehearse rig assembly, emergency protocols, and drilling procedures in a controlled virtual environment. This not only shortens onboarding time for new hires but also ensures that seasoned operators remain sharp on updated system protocols.
The combination of modular hardware and simulation-backed training forms a comprehensive upgrade package that delivers both short-term gains and long-term sustainability for land oilfield operators. Esimtech's integrated simulation technology also makes it easier to test new rig configurations, materials, and automation systems before live deployment, reducing risks and ensuring success in the field.
Sustainability Benefits
Environmental stewardship is increasingly a concern for oilfield development, and this modular system offers several advantages. Reduced fuel consumption during transport, lower emissions from shorter rig-up windows, and less waste generated from modular fabrication all contribute to a smaller environmental footprint. In addition, the integration of energy-efficient motors, recycling systems for drilling fluids, and predictive maintenance algorithms further support cleaner operations.
For oil companies looking to comply with stricter regulations or to meet internal ESG goals, this new form of oil rig design offers a compelling path forward. Modular technology doesn’t just improve performance—it modernizes field operations in a way that is responsible, scalable, and future-ready.
The Future of Oilfield Development
The Land Oilfield Equipment Upgrade Seminar made it clear: modular oil rig systems are no longer a theory—they're the new standard. From live assembly demonstrations to real-world efficiency data, it was evident that the future of oil rig construction and oil rig design lies in smarter, faster, and more adaptive systems. Modular rigs are not only revolutionizing how equipment is deployed but also reshaping operational strategies across the industry.
As oilfield companies continue to push the boundaries of efficiency and sustainability, embracing modular innovation may well be the deciding factor in staying ahead. With firms like Esimtech leading the charge, the future of land-based drilling looks not just promising—but modular, mobile, and highly optimized.